
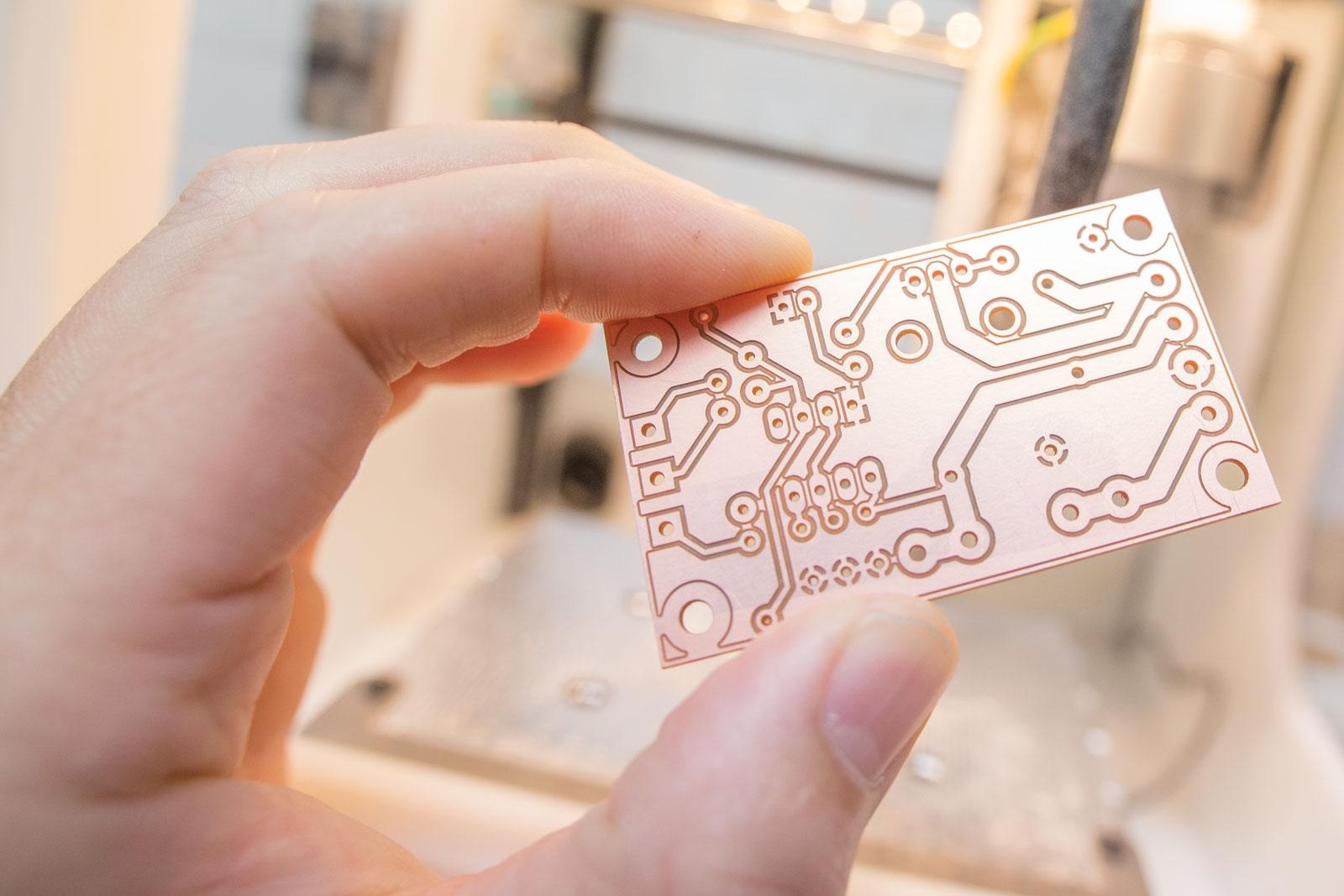
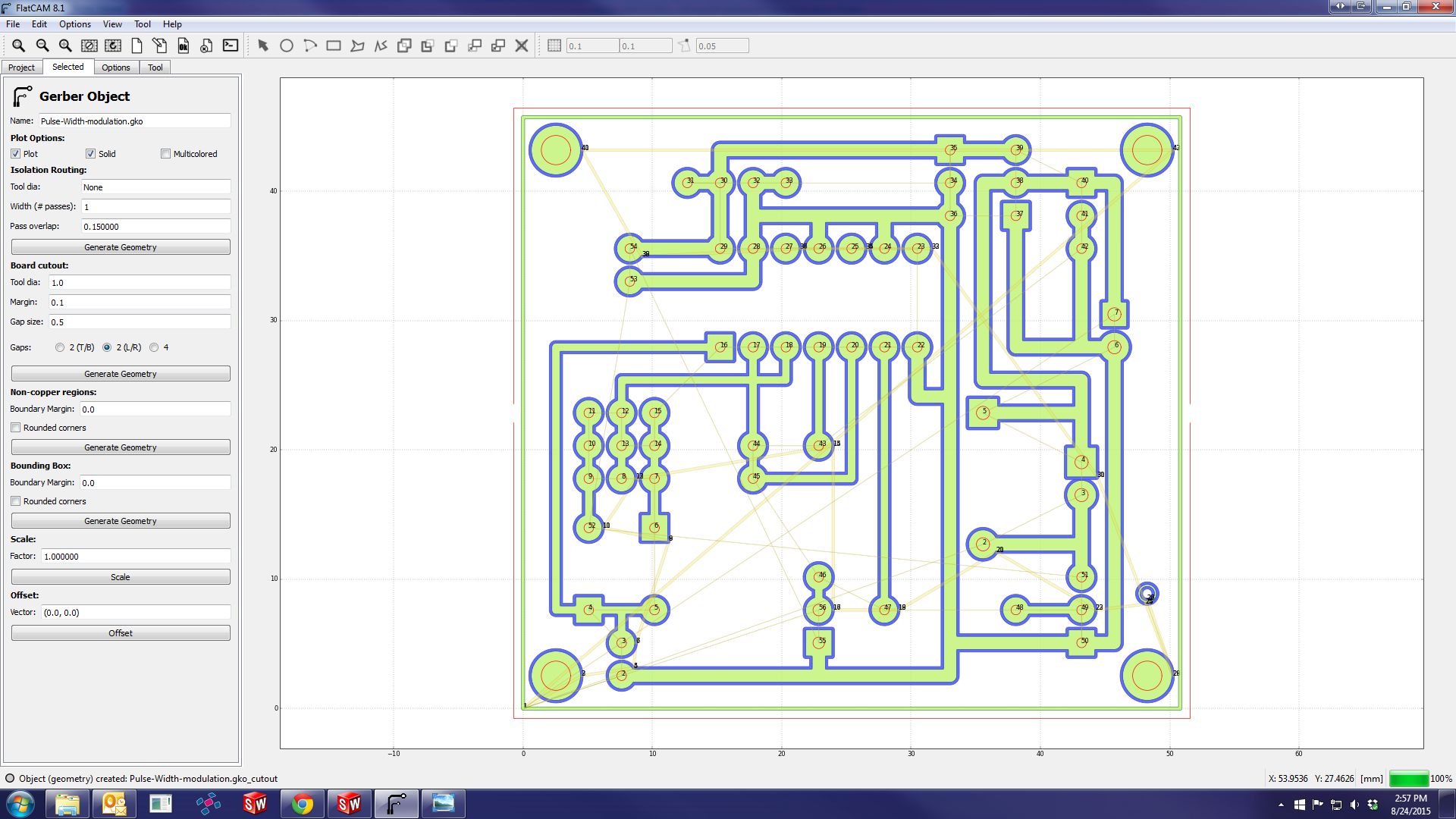

Concluding based on the implementation process, testing, and analysis are carried out that the stages for performing the Mini PCB Printing Machine assisted by Arduino board with driven by GRBL Gru can be realized according to the initial design of hardware and software design.
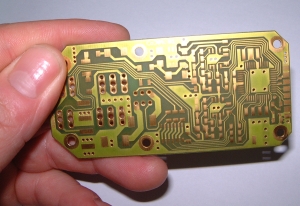
Performing the machine driving mechanism is operating tests of calibration and moving on the axes of X, Y, and Z. The miniature embodiment is carried out through (i) manufacturing and assembling to obtain the physical machine, (ii) integrating the electronic modules and all components and support systems by wiring to form an embedded system as a mini-PCB printing machine, and (iii) making a program structure based on Arduino IDE. The research methods consist of several steps to carry out each research objective. The acquisition of research contributions is expected to get the miniature embodiment of the physical machine equipped with a user program and perform the machine driver. Defining the problem formulations is related to the manufacture, assembly of the mechanical apparatus, and integrated wiring of several electronic modules. Using a microcontroller-based electronic module manufactured as desired or direct service of the board of Arduino as a control system for many purposes has become a certainty. These G-code files are then uploaded to the CNC machine using the software Universal G-code Sender, thus enabling the microcontroller to direct the rotation of motors and coordinate the movements of the end effector so as to engrave the board design on to a copper clad.Ī compact integrated circuit is an intellectual property core at the heart of the decades of embedded devices on embedded systems. The design to be engraved on the copper clad board is uploaded to a software called CopperCam, where it can be converted to G-code files after making the necessary modifications. DipTrace, an EDA/CAD software is used for creating the schematic diagram for the milled circuit boards. The end effector of the CNC milling machine has the provision to move in 3 axes-x, y and z in accordance with the input received from the controller. In this research paper we propose a computer controlled milling machine which can be used for quick fabrication of double layered PCBs called MCB where a user wants to test the circuit without the need to wait for the conventional PCB fabrication. Printed Circuit Boards (PCB) are one of the most widely used control modules in electrical and electronic industries. This research paper presents an alternative way to fabricate a Milled Circuit Board (MCB) with the help of a Computer Numerical Controlled (CNC) milling robot.
